[ad_1]
New expertise is anticipated to mass produce next-generation, customised e-textiles for healthcare, industrial and army use.
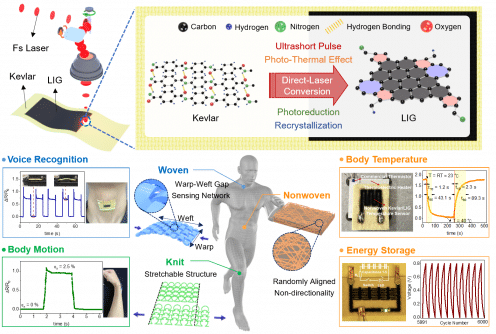
The world’s first-ever improvement of customised digital textiles (e-textiles) utilising graphene with a multimodal strategy has been achieved. Multimodal refers to exchanging data by means of numerous sensory interfaces, together with visible and auditory sensations.
Within the realm of digital textiles (e-textiles), a collaborative analysis staff led by Principal Researcher Soongeun Kwon from the Division of Nano Manufacturing Expertise on the Korea Institute of Equipment and Supplies (KIMM), an establishment falling beneath the purview of the Ministry of Science and ICT. Moreover, Professor Younger-Jin Kim from the Division of Mechanical Engineering on the Korea Superior Institute of Science and Engineering (KAIST) performed a pivotal function on this improvement. This staff pioneered the world’s first graphene-based customised e-textiles and shared their findings within the prestigious scientific journal “ACS Nano,” identified for its spectacular impression issue of 18.027.
The collaborative analysis staff achieved the fabrication of graphene-based e-textiles utilizing laser direct patterning expertise, avoiding using dangerous chemical substances or optical masks usually employed for patterning. This innovation concerned the creation of laser-induced graphene (LIG) instantly on the e-textiles. Laser direct patterning expertise creates patterns on practical supplies by directing a laser beam onto the garment’s floor, inflicting the conversion of supplies solely within the areas uncovered to the laser. When a high-power laser is utilized to the floor of a polymer movie or garment, the optical power transforms into thermal power, resulting in the instantaneous formation of carbon materials, particularly within the irradiated areas. This ensuing materials, intently resembling graphene, a two-dimensional nanomaterial, known as laser-induced graphene (LIG) as a consequence of its crystal construction similarity.
Historically, e-textiles have been produced utilizing two most important approaches: one includes making use of conductive ink to cloth to create electrically conductive textiles, that are then woven with commonplace supplies. The opposite methodology entails including a skinny, practical layer to common materials. These standard strategies have limitations when it comes to design flexibility and contain advanced processes. Moreover, there’s a danger of dangerous chemical substances being launched throughout manufacturing, which hampers mass manufacturing capabilities.
Femtosecond Laser Processing Expertise
This expertise makes high-quality Laser-Induced Graphene (LIG) supplies with top-tier electrical conductivity effortlessly produced by directing a laser beam onto cloth surfaces. An important good thing about this strategy lies in its eco-friendliness, because it eliminates the necessity for chemical substances or further processes in manufacturing e-textiles. Moreover, {the electrical} conductivity of LIG electrodes has been achieved by making use of femtosecond laser processing expertise. Femtosecond laser processing expertise includes fabricating supplies utilizing ultrashort laser pulses characterised by extremely transient pulse width and excessive peak energy. In distinction to different laser varieties, this expertise minimises materials injury and is especially beneficial for creating high-resolution patterns.
This newly developed expertise holds promise for numerous purposes sooner or later, together with manufacturing industrial and army clothes for private well being monitoring and producing customised “sensible” clothes inside the healthcare sector. The researchers declare that this expertise emerged from a meticulous evaluation of standard cloth constructions, which had been then translated into superior graphene-based supplies with splendid e-textile properties. This innovation is of great significance, because it allows the mass manufacturing of customised e-textiles by means of an environmentally pleasant and simple course of. It’s price noting that this analysis obtained help from the “improvement of nano-based ‘Omni-TEX’ manufacturing applied sciences” mission, which is amongst KIMM’s foundational initiatives.
[ad_2]